Step-by-Step Guide to Making Calcium Grease
- Lubechem consultant
- Jun 3
- 4 min read
Calcium grease is widely used in various industries due to its excellent water resistance, high load-carrying properties, and stability at elevated temperatures. Whether it’s for automotive applications or industrial machinery, knowing how to make calcium grease can help you save costs and ensure quality. This blog post will guide you through the process step by step.
Understanding Calcium Grease Manufacturing
Before delving into the manufacturing process, it's essential to understand what calcium grease is. Calcium grease is a type of soap-based grease, derived from the reaction between a fatty acid and calcium hydroxide. This superior grease is known for its ability to withstand high temperatures and repel water, making it an ideal lubricant for various applications.
For those keen on the technical aspects, the calcium grease manufacturing process involves several critical steps that ensure the quality and performance of the final product.

Ingredients Needed for Calcium Grease
To create high-quality calcium grease, you'll need a specific set of raw materials. Here’s a breakdown of the essential ingredients:
Base Oil: Mineral oils or synthetic oils serve as the primary lubricant.
Thickening Agent: Calcium soap is the main thickener for calcium greases.
Additives: Various additives like antioxidants, rust inhibitors, and anti-wear agents can enhance the grease's properties.
When choosing your ingredients, ensure they meet industry standards for the intended application. Using high-quality base oils can significantly impact the final product's performance.
The Calcium Grease Manufacturing Process
Now, let’s dive into the step-by-step process of making calcium grease.
Step 1: Preparation of the Thickeners
Start by preparing the thickener. This involves mixing calcium hydroxide with water at a specific concentration. Gradually incorporate fatty acids into this mixture, maintaining a consistent stirring to ensure they dissolve uniformly. The reaction between the calcium hydroxide and fatty acids results in the formation of calcium soap.
Step 2: Heating the Mixture
Once the thickener is ready, you’ll need to heat the mixture to facilitate the reaction. The ideal temperature for this reaction is around 70-80 degrees Celsius. During this stage, monitor the temperature closely to avoid overheating, which can cause the soap to break down.
Step 3: Mixing with Base Oil
After achieving the right consistency, the next step is to mix the thickener with the base oil. This is best done in a high-shear mixer to ensure a smooth and homogeneous mixture. The quantity of base oil will depend on the desired consistency of the final grease.

Step 4: Adding Additives
As you mix the base oil and thickener, it’s time to incorporate the various additives you prepared earlier. This may include anti-wear agents that enhance performance under heavy loads, as well as rust inhibitors to protect machinery. Ensure each additive is mixed thoroughly into the grease blend.
Step 5: Cooling and Consistency Check
Once all ingredients are combined, allow the grease to cool. After cooling, it’s crucial to check the consistency. The final product should be smooth and homogenous, free from any lumps or defects. Adjust the proportions of base oil or thickener if necessary.
Step 6: Packaging the Calcium Grease
After achieving the desired consistency, the last step is to package the calcium grease properly. Use clean, airtight containers to preserve the freshness and prevent contamination. Label each container with the date of production, product specifications, and safety information.
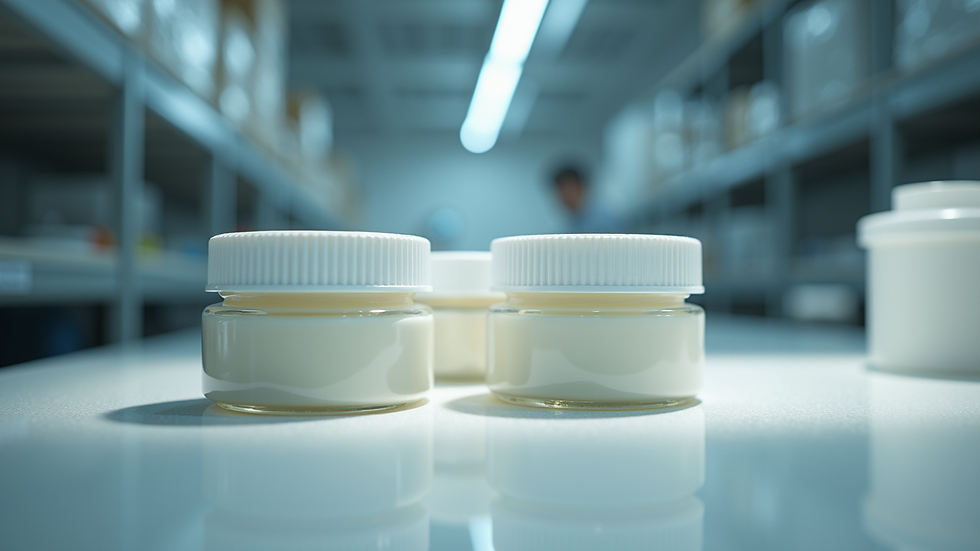
Best Practices for Calcium Grease Manufacturing
To achieve the best results in calcium grease manufacturing, consider the following best practices:
Maintain Cleanliness: Always work in a clean environment to avoid contamination.
Quality Control: Regularly test your final product for consistency and performance.
Training: Ensure all team members involved in the process are trained and understand the importance of each step.
Applications of Calcium Grease
Calcium grease is versatile and can be used in various applications, including:
Automotive: Lubricating wheel bearings and chassis components.
Industrial Machinery: Perfect for equipment that operates under high moisture conditions.
Agricultural Equipment: Used in tractors and other machines exposed to the elements.
Each application may have its specific requirements, so always consult guidelines or seek expert advice when necessary.
Common Challenges in Calcium Grease Manufacturing
As with any manufacturing process, there are challenges you may encounter. Here are a couple of common issues:
Inconsistent Texture: This can arise from improper mixing or the wrong ratios of ingredients.
Degradation of Properties: Understanding the chemistry involved can help in preventing loss of properties like load-bearing capacity or water resistance.
When faced with these challenges, review your process, confirm the quality of your raw materials, and make necessary adjustments.
Emerging Trends in Calcium Grease Manufacturing
The industry is evolving, and new trends are emerging in calcium grease manufacturing:
Sustainability: Many manufacturers are shifting toward bio-based raw materials to reduce environmental impact.
Enhanced Performance Additives: Research into new additives continues, leading to greases with improved performance in extreme conditions.
Staying updated on these trends can help you maintain a competitive edge in the market.
Final Thoughts
Making calcium grease can be a rewarding experience, especially when you understand the intricacies involved in the manufacturing process. By following this guide and adhering to best practices, you can create high-quality grease suitable for various applications. Whether for home use or industrial applications, mastering calcium grease manufacturing will serve you well in various capacities.
Comments